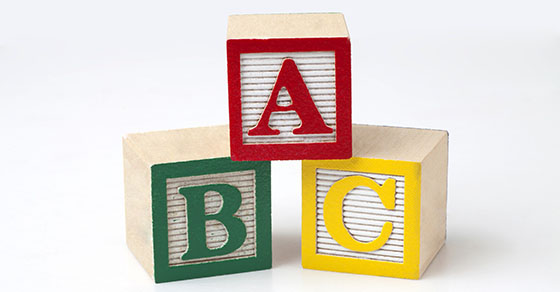
Revenue and expenses, as reported on your company’s income statement, have limited usefulness to people inside the organization. Managers often need information presented in a different format in order to make operational and strategic decisions. That’s where activity-based costing comes into play. This costing system is commonly used in the manufacturing and construction sectors to determine which products and customers are profitable, to identify and eliminate waste, and to more accurately price products or bid jobs going forward.
4 steps
With activity-based costing, you assign cost codes (think of them as price tags) to each activity completed based on the resources consumed. These cost codes define the activity; the equipment, materials and labor used to complete it; and how long it takes to finish the task.
Here are four basic steps used to create a cost code in activity-based costing:
1. Identify activities. Create a list of tasks your company performs to complete a job. Define each activity in such a way that there’s no overlap between them.
2. Allocate resources. For each activity, list resources used. These include material, equipment, labor hours and, if applicable, subcontracting costs.
3. Calculate the per-unit cost of each resource. Choose a standard, measurable unit of each resource and calculate the cost per unit. Sometimes, you’ll have to calculate an average cost based on purchase receipts for a specific period. For example, if a box of screw anchors holds 100 and costs $30, the per-unit cost of screw anchors would be 30 cents if you consider one “unit” to be a single screw anchor. For labor hours, the measurable unit would be the wage paid per hour.
4. Determine how much of each resource is used for each activity. Multiply the per-unit cost of each resource by the number of units consumed. Add indirect costs to determine the total cost. These may include rents, machinery payments, salaries and other expenses that don’t directly contribute to completing an activity.
Potential benefits
Companies can use activity-based costing to learn what’s working — and what’s not. For example, let’s say a job is costing more than it should, or is taking too long to complete. Activity-based costing will quantify for each task: 1) the materials consumed, 2) which pieces of equipment were deployed, and 3) how many labor hours were spent to complete it. This process allows you to track the progress of jobs in real time, so you can correct mistakes and inefficiencies before losing money to them.
You also may be able to uncover excessive spending trends, so you can better control purchasing. For strategic planning purposes, the process can provide a clearer picture of what types of activities and jobs will likely boost the bottom line and enable you to grow your business. Likewise, it can help assess whether your current product mix needs to be modified to boost profits.
Furthermore, with price tags attached to everything, estimators can “cut up” a prospective job into well-defined activities and then calculate estimates for each of those tasks, resulting in a more accurate overall project estimate. If the scope changes, thereby increasing or decreasing the number of activities, it’s much easier to recalculate the estimate. Activities essentially become line items that can be added or deleted.
One size doesn’t fit all companies
Activity-based costing can be used to supplement, but not replace, your company’s traditional cost accounting system. Although this process may seem confusing, software solutions can help shorten the learning curve. Contact us to learn how your business can benefit from activity-based costing and how to effectively implement this process based on the nature of your operations.
© 2022
Checkpoint Marketing for Firms
THOMSON REUTERS